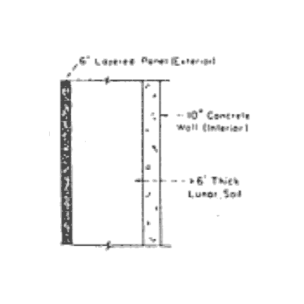
Dr. T. D. Lin, a native of Taiwan, is now living and working in this country for Construction Technology Laboratories in Skokie, Illinois wants to build a lunar base out of concrete. In order to have done his homework in connection with the World Space Foundation bid for a small amount of Apollo sample return moon dust for an experiment in making concrete using lunar materials.
Since the sample was too small for actual experiments with lunar highlands soil simulant, rich in aluminum and calcium, to prepare his “cement” and using raw simulated regolith in place of sand and aggregate to serve as filler, he made his batch of concrete. It worked fine.
Now that he experimented down pat, he tried it using the real thing. Combining water, cement, and his ounces of moon dust he produced a more realistic lunar concrete that proved to be considerably stronger than ordinary cement on terrestrial soil.
“We measured its compressed strength at 10,971 psi compared to 7,900 psi for a comparable terrestrial concrete,” Lin reported. The concrete slab is standard for a reinforced concrete slab is 4000 psi. The results were very encouraging.” Lin believes the angular shape of most particles that make up the lunar regolith (as they have never been exposed to weathering by wind or water — only create erosion by thermal cycling and micrometeorite bombardment) is responsible for the increased strength.
Lin now heads up his own company, the Lunar Development Council (LDC), whose logo is a crescent moon with a steam shovel poised on the bottom cusp. Lin has designed a large concrete lunar base, 210 feet in diameter. The three floor round concrete structure would provide 90,000 square feet, with all of the walls coming from the Moon. Except for 55 tons of hydrogen which would come from Earth, in addition to the cement to be processed from highland regolith, raw lunar materials would be used for shielding as well as for aggregate.
The walls of each floor would consist of two layers of interlocked together. The inner layer, a cross maze of cables under tension in concrete, is stronger under compression than it is under tension, the 18″ thick convex panels work in combination with the cable stays. An outer wall of 6″ thick concrete and under prefixed would provide a surrounding bay to be filled with a minimum of 6′ of regolith shielding, more piled on the roof. Iron extracted from the soil would be processed not only into the tension cables but into helping connect two joining the convex panels forming the inner pressurized wall and the concave outer panels holding in the regolith shielding.
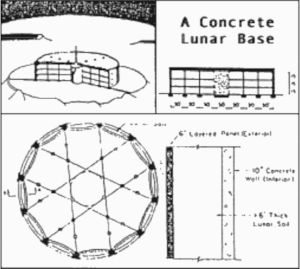
Lin’s collection of Earth-made modules to assemble into a prefab ready-to-occupy outpost, with the good intentions of somebody working towards some early industrial projects, Lin’s group would start with lunar industry gingerly. To process the his steel cables and panel connectors, his concrete and convex inner panels, etc. The outpost itself would be the first project.
At its controls and in all other aspects, “much of others” we have discussed. The LDC base, once finished would not look much different as everything would be in place to make additional pressurized structures. You have to wonder if Lin’s approach is the wave of the future, where everyone else has the cards and the horse lined up. This approach would make them leap to a turn-key approach. LDC would build the Moonbase and then turn it over to NASA or a comparable operator who could then concentrate on operations: prospecting, exploring, and science experiments.
At 90,000 square feet, equivalent to a square one floor structure 300′ on a side, this one structure would provide plenty of space for a small town. Lin envisioned a longer term plan to extend outwards by sintered blocks. Lin also expressed a desire to repeat his experiments with simulated Mars soil. And he thinks he can cut down the water content and make it to a hydrated cement needed if planned experiments prove concrete by sintering raw ingredients instead of soaking them work as he expects.